Day 1 :
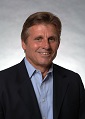
Biography:
Charlie Duncheon is the Co-founder and Advisor of Grabit, Inc. He has more than 25 years of senior management experience in leading the growth of start-ups to successful companies. He has served on several Board of Directors including the Robotics Industries Association and Automation Technology Council. In 2000, he received the Robotic Industries Association Joseph Engleberger Leadership Award. Previously, he was elected President of the Robotics Industries Association, and served as the U.S. National Chairman for the United Nations International Federation of Robotics. He received his MBA from Southern Illinois University and his BS in Industrial Engineering from Purdue University.
Abstract:
The industrial robot industry has experienced steady growth for the last four decades. Certain technologies like machine vision have enabled that growth. Today, there are multiple enabling technologies that are allowing even faster robotics growth. The enabling technologies will be covered including sensing, new robotic mechanical form factors, and artificial intelligence. These key technologies will be described in depth and how they are enabling faster robotics growth. The exciting impact these enabling technologies will have on robotics going well beyond the factory floor will be discussed. The speaker will also address technologies that not only expand robots to new applications but lower the total life cycle costs of robots.
- Track 1: Automation Technologies
Track 3: Control and Mechatronic Systems

Chair
Juan R Pimentel
Kettering University, USA

Co-Chair
Cameron Gieda
Sick Inc., USA
Session Introduction
Juan R Pimentel
Kettering University, USA
Title: Context aware systems for unstructured environments based on WSNs
Time : 11:00-11:30
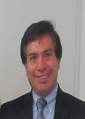
Biography:
Juan R Pimentel is a Professor of Computer Engineering at Kettering University in Flint, Michigan, USA. He is an expert in the area of Internet of Things, Industrial Internet, safety-critical systems and industrial computer networks, particularly issues related to real-time protocols, safety-critical protocols, dependable automotive embedded distributed systems, and distributed industrial and embedded systems. He is a recognized international expert in the area of industrial communications and real-time and dependable protocols. He has written 3 books on networking, multimedia systems, and safety critical systems. He has worked with major manufacturing and process control projects involving products from companies such as Siemens, Rockwell, Schneider Electric, ABB, and GE-Fanuc. As a 1980 graduate of the University of Virginia, his accomplishments include the co-development of the application layer for Profibus (with Siemens), and the development of FlexCAN, a CAN-based safety-critical architecture. In 2007 he received the “Distinguished Researcher Award†from Kettering University for contributions in the area of industrial communication systems and automotive systems. During the last few years he has been involved with wireless sensor networks (WSNs), telemetry systems using TV white spaces, software define radios (SDR), and platforms for deploying IoT technologies. He is currently writing a book on “Industrial Internet Connectivityâ€.
Abstract:
There is significant work done in the area of context aware for structured environments such as homes, buildings, manufacturing, and others similar. However, as transformative initiatives such as the Internet of Things (IoT) take hold, we are dealing with environments that are not so well structured such as the ones mentioned above. One example of such unstructured environments is the vast amount of data gathered by wireless sensor network (WSN) that might have thousands of tiny sensors collecting many sorts of data. In such a case, just about every element of a traditional context aware system must be re-considered. In this talk, we will review the characteristics and features of context aware systems for well structured environments, the characteristics and features of WSNs, and present a set of requirements for context aware systems suitable for unstructured environments based on WSNs.
Cameron Gieda
Sick Inc., USA
Title: Industrial automation technologies and the realization of factory 4.0
Time : 11:30-12:00
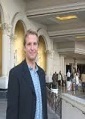
Biography:
Cameron Gieda is an Automation Specialist with over 20 years of experience designing and selling automation systems and technologies for some of the world’s top automation companies such as Keyence, Omron, Honeywell, Emerson, Fluke and now Sick Inc. In my current role in Silicon Valley he collaborates with companies ranging from consumer electronics, automotive, semiconductor, biomedical and aerospace. Key areas of interest are machine vision, 3D Vision, Safety devices and optical inspection.
Abstract:
Industry 4.0 is an initiative actively funded by the German government in collaboration with a number or European manufacturing technology companies. The goal of this initiative it to develop the technological foundation for "smart factories†using industrial networks/SCADA systems to gather, process and position data from a network of distributed intelligent via sensors. From our perspective at Sick Inc. a large German optical sensing can safety company, we will help realize the smart factory through distributed intelligent in what were previously simple sensors. Newly developed industrial networking methods allow more information to be pulled from smaller and more remote devices. Think Internet of Things. Moreover, these devices can be controlled and adjusted remotely, which eliminates a very time consuming maintenance operation. Simple photo electric sensors can now gather information far beyond part presence and are able to track the time of a specific event, report issues downstream to other sensors and make a decision as to how best to detect certain objects. This has resulted in other benefits such as miniaturization of product because they no longer buttons, indicator LED’s or displays. These sensors can also provide predictive maintenance information as they can send out a message before they fail so sensor replacement can be scheduled when the line is not running. The method by which this data is transmitted is also very important and we see the developing EtherCat standard as a great fit for factory floor communications. EtherCat provide a singular “clock†on which every sensors are running so for high speed positioning application using interrupt sensors to gauge position or size can be much more accurate. This is also evolving into a safety communication standard, which is slowly being accepted by the U.S. and European front end semiconductor machine manufactures.
Utku Buyuksahin
Sensobright Industries LLC, USA
Title: BTSS – BUYUKSAHIN tactile sensing system
Time : 12:00-12:30
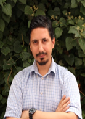
Biography:
Utku Buyuksahin received the BS and PhD degree in Mechanical Engineering from Yildiz Technical University, Istanbul, Turkey in 2004 and 2010 respectively. He received another BS degree in Business Administration in 2007. His main interest areas are; robotics, sensors, image processing and motion control. He has received many awards and has over 30 technical publications, including a book and a book chapter. He holds total number of 6 patented and patent pending inventions. He has accomplished over 70 projects (all mechanical designs, manufacturing, electronic designs and applications, software developments) including, 3 axes CNC Milling Machine, 6 DOF. Stewart Platform for 8D Cinemas, Vehicle simulators, 11 DOF.Hepa Filter Test Robot etc.
Abstract:
The desired level for tactile sensing in robotics and devices compared to the human’s tactile sensing ability still could not be reached because there are 241 sensory receptors per centimeter square in human’s tactile sensing and the acquired data is delivered to human brain without any data loss. But on the contrary the sensory receptors of robotics and devices for tactile sensing are at the number of tens per centimeter square and if total sensory number is increased to hundreds or thousands, the acquired data cannot be delivered to the computer properly or it will cost a lot. Due to our patented invention “Multi Point, High Sensitive Tactile Sensing Module for Robots and Devices†(US9030653B1), the number of tactile sensory receptors per centimeter square can be increased up to one million. The system also has the ability of temperature measurement in case needed. The key features of the system are as follows: System sends the gradual (not only I/O) tactile sensing data of each sensor individually and real time over a single USB cable which can reach up to total of 50 M+ sensor data with only 1 USB cable. System is constructed of all bendable materials which give us the chance of covering non-uniform shaped mechanical systems.As the tactile sensing and temperature data is transferred by light, the system does not interfere with magnetic fields. The systemis built up with only over-the-counter components that are common and easy to provide.
Sami A Alhasan
The Excellency Center of Water Technologies, Saudi Arabia
Title: Automating farms irrigation in Saudi Arabia
Time : 13:30-14:00
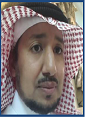
Biography:
Sami A Alhasan did his B.S. Degree in Systems Engineering from King Fahd University of Petroleum and Minerals, Saudi Arabia in 1990. Then in 1994 he got his M.S. Degree in Electrical Engineering from Georgia Institute of Technology, USA. Later in 1999 he got his Ph.D. in Electrical Engineering from Georgia Institute of Technology, USA. Topic of thesis is “Intelligent Approaches to Mission Planning and Control of Autonomous Vehicles.†Currently he works as Head of Strategic Partnership Program between Technical Vocational Training Corporation (TVTC). Vice Chairman of GE Technical Academy – Saudi Arabia.
Abstract:
This paper presents a large-scale project under implementation in the Eastern Province of Saudi Arabia where a conventional manual irrigation system of almost 24,000 farms has been automated and interlinked with a global SCADA system for the purpose of using scarce water resources more efficiently, and to utilize technology to support agricultural development. The paper explains the approach for automating this huge irrigation network and the implemented control and SCADA systems. It, then, highlights implementation findings and avenues of study and research.
Walter Dunkmann
J Schmalz GmbH, Germany
Title: Intelligent vacuum technology in automation
Time : 14:00-14:45
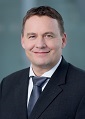
Biography:
Walter Dunkmann is Head of R & D and Business development for process automation end-effectors at J. Schmalz GmbH. Earlier he has worked as a Controls engineer. Many years he worked as a Project Manager for process automation in automotive industry and Sales & Product Management at ABB Robotics. Also he experienced as a Head of Business unit Press Automation at KUKA Systems
Abstract:
Experts agree that in the future, no company competing at an international level can afford to ignore Industry 4.0. Today, enterprises need to set a course for tomorrow and be ready for networked production. People, machines and resources interact in the factory of the future. Strongly individualized products are created through highly flexible and resource-efficient production. There is extensive integration of customers and business partners and value-added processes. Schmalz has already started along this path and is supporting their customers with innovative and future-proof solutions. Our work was focused on intelligent process communication long before any mention of Industry 4.0. In 2008, we launched the world\\\\\\\'s first vacuum generator with IO-Link interface, making it Industry 4.0 ready. Today we are the first manufacturer to combine sensor and actuator functions in a 4.0 compatible device. The ultimate aim of all our efforts and activities is to help our customers achieve more productive, efficient and flexible production processes through the use of intelligent vacuum solutions, thus enhancing their ability to compete.
Charlie Duncheon
Grabit, Inc., USA
Title: Reaching Ultimate Flexibility for Robot Grippers
Time : 14:45-15:15
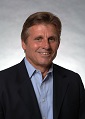
Biography:
Charlie Duncheon is the Co-founder and Advisor of Grabit, Inc. He has more than 25 years of senior management experience in leading the growth of start-ups to successful companies. Duncheon has served on several Board of Directors including the Robotics Industries Association and Automation Technology Council. In 2000, he received the Robotic Industries Association Joseph Engleberger Leadership Award. Previously, he was elected president of the Robotics Industries Association, and served as the U.S. National Chairman for the United Nations International Federation of Robotics. Duncheon received his MBA from Southern Illinois University and his B.S. in industrial engineering from Purdue University.
Abstract:
Since the beginning of robotics until today most robots in assembly and handling automation are equipped with part-specific grippers. Typically, these grippers are mechanical or vacuum in form factor. This approach does not work with high mix applications. One example of a high mix application is in the order fulfillment market for E-commerce order fulfillment. This talk will address the challenge in more detail, technology limitations in meeting the challenge, and new developments that hold promise to truly build a flexible robot gripper for very broad ranges of products.
Jaya Bhanu Rao Degala Ramalu
Newcastle University, UK
Title: Static and dynamic obstacle avoidance behaviour for powered wheelchair control system
Time : 15:15-15:45
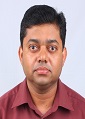
Biography:
Jaya Degala is currently pursuing his Doctoral studies in the field of intelligent Mechatronics control under the School of Mechanical and Systems Engineering, Newcastle University, United Kingdom. He has completed his Diploma Studies in the field of Industrial Automation at German-Malaysian Institute, Kuala Lumpur, Malaysia in 1997. He also holds a degree in Mechatronics Engineering from University of Leeds, United Kingdom in 1999. He obtained Master’s Degree in Mechatronics at Newcastle University, United Kingdom in 2003. Then, he worked as a Lecturer at German-Malaysian Institute Kuala Lumpur, Malaysia for 5 years. After that, he continued working as a Lecturer at Universiti Kuala Lumpur, Malaysia for another 5 years, majoring in Mechatronics subjects. He has successfully designed and patterned Automatic Multi-Peeler Machine. He also completed a project on Automatic Tyre Inflation System for vehicles.
Abstract:
Disabled and elderly people are to manoeuvre the powered wheelchair smoothly due to frail and lack in dexterity in handling joystick movement. Wheelchairs users require efficient transition in preventing and avoiding collisions to minimise fatigue and to reach destination safely. The collision cone approach has been proven to avoid static and dynamic obstacles successfully by researchers in mobile robots. This paper proposes an improvement to the static and dynamic obstacle avoidance behaviour for non-holonomic semi- autonomous powered intelligent wheelchair control system. The velocity obstacle approach (VO) is proposed because it is considered an easy and simple method for avoiding dynamic obstacles while collision cone approach is used to detect collision situation between two circular shaped objects. However, the challenge takes place in detecting non-circularshaped objects from sensor data. The collision avoidance behaviour has been further improved with integration of collision cone approach and fuzzy inference system. Experiments on various environmental scenarios such as partly cluttered areas have been demonstrated with the aid of player/stage simulation on Ubuntu12.04 LTS. A Saitek Cyborg Evo wireless joystick with 6 axes is used to drive the wheelchair in the player/stage simulation. The experimental results show significant improvement in detecting and avoiding collisions.
Jone F Chen
National Cheng Kung University, Taiwan
Title: Use of data analysis and TCAD simulations to understand the characteristics and reliability of high voltage MOS transistors
Time : 15:45-16:15
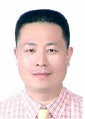
Biography:
Jone F Chen received the PhD degree in Electrical Engineering from the University of California, Berkeley. He worked in the Department of Electrical Engineering and Institute of Microelectronics, National Cheng Kung University, Tainan, Taiwan for more than 15 years, where he is currently a Professor. He has published more than 50 papers in reputed journals.
Abstract:
High voltage metal-oxide-semiconductor (MOS) transistors are widely used in smart power management integrated circuits (IC), liquid-crystal display (LCD) drivers, and NAND flash memory periphery circuitry because of the compatibility to be integrated into standard complementary metal-oxide-semiconductor (CMOS) process. Because high voltage MOS transistors are operated under high voltage, breakdown voltage is a critical device parameter and hot-carrier induced device degradation is an important reliability concern. One key factor to affect breakdown voltage and hot-carrier induced device degradation is the process to fabricate drift region of the device. This paper reports analysis of breakdown voltage and hot-carrier induced device degradation in high voltage MOS transistors. The process to fabricate drift region of high voltage MOS transistors is varied to examine its impact on breakdown voltage and hot-carrier-induced device degradation. Not only experimental data but also technology computer-aided-design (TCAD) simulation results are analyzed to understand the underlying physical mechanisms. Our findings reveal that care should be taken in determining the fabrication process of drift region because a trade-off between breakdown voltage and hot-carrier induced device degradation is observed.