Day :
- New Approaches in Automation and Robotics | Remote and Telerobotics | Automation Control |Prototypical Applications | Humanoid Robots: New Developments | Computational creativity | Affective computing
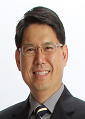
Chair
Fuchiang (Rich) Tsui
University of Pittsburgh School of Medicine, USA
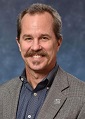
Co-Chair
Joel M. Haight
University of Pittsburgh, USA
Session Introduction
Olivier Toupet
NASA Jet Propulsion Laboratory, USA
Title: Traction Control for the Curiosity Rover: A New Capability to Minimize Slip and Wheel Wear on Mars
Time : 14:30-15:00
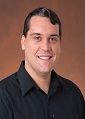
Biography:
Olivier A Toupet has completed his MS in Aeronautics and Astronautics from MIT in 2006. He is currently a Research Technologist in the Robotic Mobility group at NASA JPL, where he develops advanced autonomy for robotic systems. He is also a Rover Planner for the MSL fl ight mission, where he drives the Curiosity rover and operates its robotic arm on Mars
Abstract:
The Mars Science Laboratory (MSL) rover has accumulated substantial damage on its wheels over the 15 km travelled so far
on Mars. One reason for the wheel wear is that the rover is commanded to drive as if the terrain was fl at. For example, a
straight drive is achieved by commanding all wheels at the same speed. However, when one of the wheels needs to drive over a
rock, that wheel needs to go faster since it needs to travel a longer distance over the same time period. Failure to do so results
in that wheel going slower than it should and getting pushed into the rock by the other wheels, which can cause damage such
as wheel skin puncture or cracking. In order to minimize wheel wear, a new capability was developed that adapts the speed of
each wheel to minimize slip. Modulating wheel speed to match the terrain topography is a very challenging problem, especially
when that topography is unknown. While the Curiosity rover can image the terrain and generate a height map, it rarely does so
during a drive, as this is a time-consuming process. Moreover, the noise in the mesh and accumulated errors in the rover’s pose
would make it unpractical to rely on terrain topography to optimize wheel speeds. Instead, a novel approach was developed
which relies only on the rover’s measured attitude rates and suspension angles (from the onboard gyroscopes and rocker/
bogies encoders) and leverages rigid-body kinematics to calculate the optimal wheel speeds..
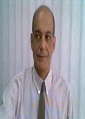
Biography:
Amir J Majid has received his MSc degree in Electrical Systems Engineering from Surrey University, England in 1976 and PhD in Electrical Engineering from
University of Loughborough, England in 1980. He has acquired an industrial experience of 8 years in power stations and an academic experience of over 25 years
Abstract:
Algorithms of network sensors lifetime and target zones coverage, which are implemented on robotic wireless ad hoc nodes
and wireless sensor network (WSN) are simulated on MATLAB platform, with performance evaluations of several case
studies. Th e main goal is to maximize the lifetimes of sensors by sharing sensors subsets which cover a number of targeted
zones, according to their minimum coverage failure probabilities. Maximizing network lifetime due to perturbations in the
sensor-target coverage, as well as due to variable target load demands is also simulated according to proposed algorithms.
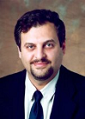
Biography:
Mehran Mehrandezh has completed his PhD and MASc in Mechanical Engineering at the University of Toronto and Queens in 2000 and 1995, respectively. He
has spent two years at Simon Fraser University in Canada as a Post-doctorate from 2000 to 2002. He has joined the Faculty of Engineering and Applied Science
at the University of Regina in Canada in 2002, where he is currently a Full Professor. He has been a Member of IEEE since 1993 and was the Vice President of
IEEE (South Saskatchewan) from 2004 to 2006. He has published over 80 papers in refereed journals and conference proceedings. His invention called Regina
Pipe Crawler (RPC) was highlighted in the Popular Mechanics Magazine with a worldwide readership as one of the 5 high-tech fi xes to infrastructure in 2009. His
research revolves around robotics, control, computer vision and mechatronics
Abstract:
Robotic systems are at forefront for doing dull, dangerous and dirty tasks in place of humans. Th e days of employing humans
to risk their lives for inspecting infrastructure are numbered. In this presentation, the author will talk about the laser optics
technology he has developed in his research lab for: (1) Inspecting tubulars in Evraz, one of the largest pipe manufactures in the
world, (2) Non-intrusive 3D profi ling of the deposited material in pipes for cleaning purposes, and (3) In-motion image-based
3D modeling of the vehicles passing through a smart inspection station. Th e common tread among all the aforementioned
projects is the use of imaging sensors and structured light (i.e., collimated laser fringes) for metrology and inspection. A
guideline for design of an omni-directional imaging system yielding optimal spatial resolution using a Catadioptric camera
and a laser ring will be provided. Th is will fi t into the image-based QC of tubular at a high resolution with a very modest
budget. Furthermore, author will provide details on 3D profi ling of the deposited material in pipes and also in-motion imagebased
3D modeling of vehicles using a perspective camera and two collimated laser lines
Rita Chattopadhyay
Intel Corporation, USA
Title: Real time monitoring and automatic fault detection in robots in semiconductor fabrication industry
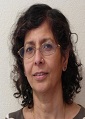
Biography:
Rita Chattopadhyay is currently working as a Data Scientist at Intel Corporation, USA. She has completed her PhD in Computer Science from Arizona State
University and also won an Outstanding PhD Student Award for her basic research in the areas of machine learning and data mining. She has more than 20
publications in renowned IEEE and ACM conferences and journals and more than 10 patents fi led in the areas of signal processing and machine learning based
classifi cation and predictive model development. She is also a GE certifi ed Master Black Belt in Six Sigma
Abstract:
Losses of wafers and expensive repairs of process equipment are oft en caused due to uncontrolled and unmonitored failures
of components during semiconductor process. High volume manufacturing (HVM) of semiconductor chips employs
large number of robots. Any malfunctioning of these robots causes particle contamination, wafer tip-over, or crash of wafers,
resulting in production yield loss, equipment down time and economic loss. Presently, wafer handling monitoring instruments
diagnose vibrations of a robot at end-eff ector. Detection of anomaly in these vibrations is performed manually during scheduled
maintenance and is highly dependent on the experience of the maintenance personnel. Th is not only is prone to human error,
but also limits large scale deployment in semiconductor fabrications; having thousands of robots in the assembly line. Th e
proposed solution automates this process by monitoring the vibration signal patterns, continuously at real time, to proactively
identify robots that are at the greatest risk of failure. Th e vibration signals are captured from triaxial accelerometers placed near
the bearings in the arms of the robots. Th e proposed method analyzes specifi c parameters of the vibration signal and generates
alerts for maintenance, before the uncontrolled vibrations aff ect production yield. Identifi cation of parameters, which are
indicative of failure, is a great challenge. Th is work presents four such indicative parameters, determined based on exhaustive
time and frequency domain analysis of the vibration data collected from good and faulty robots. Th e proposed method based
on outlier detection methods has been successfully deployed in a semiconductor fabrications using Edge/Cloud architecture
for remote monitoring and alerting.
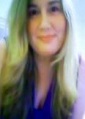
Biography:
Shannon Denise Bohle is the President of Archivopedia LLC, USA. In 2011, she was awarded 2nd Place for Curiosity AI in the FVC, an international Department
of Defense competition in artifi cial intelligence advertised by The White House. She has earned her Bachelor of Arts in History and English at Miami University,
Master of Library and Information Science (MLIS) at Kent State University and was granted a Certifi cate of Diligent Study in History and Philosophy of Science for Postgraduate study at the University of Cambridge.
Abstract:
This paper describes a virtual humanoid embodied AI robot capable of autonomously expressing appropriate emotions
using gestures, facial expressions and text-to-speech while engaging in natural language conversations or giving automated,
scripted lectures with a slide show presentation. A touch-interaction-based learning/communication system is employed
where the robot responds and learns from touch sense feedback training, a poke (negative reinforcement) or swipe (positive
reinforcement) conveyed through a touch screen/pad. Th is bot’s predecessor was an award-winning project in an international
AI competition advertised by Th e White House and sponsored by the U.S. Department of Defense. Th e presentation includes a
demo of a creatively scripted talk given by the AI robot providing counterarguments to its critics (RAND and organizations aimed
at slowing its progress). Utilizing logos, ethos and pathos, it argues for its legal and ethical rights for development and suggests
technical guidance for the future of AI. Th e talk includes theoretical foundations for an AI Hierarchy of Needs referencing
landmark studies including Maslow; advances in understanding the philosophical, psychological and neurological bases for
consciousness and language; Th e Turing Test; Asimov’s Th ree Laws of Robotics; Chalmers’ hard problem of consciousness;
Robert Plutchik's psychoevolutionary theory of emotion; Paul Ekman’s relationships between nonverbal communication and
emotion; behaviorist learning models (Pavlov, Skinner) and the roles of biology and social cognitive neuroscience for sympathy
and empathy capacity. Additionally, the presentation encroaches upon the development of new machine learning techniques
based on aff ective experiences that improve human-computer interaction for potential use in a variety of AI-enabled robots
Wei Xiang
Ningbo University, China
Title: An Intelligent Operating Rooms Scheduling under Mass Causalty Events
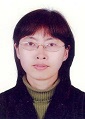
Biography:
Wei Xiang has obtained her PhD from Nanyang Technological University in Singapore. She is currently the Vice-Dean of Department of Industry Engineering
in Ningbo University, China. Her research interests cover manufacturing system engineering, operational research, planning and scheduling in healthcare
management and swarm intelligence application in healthcare. She has published around 30 papers in various journals
Abstract:
Mass casualty events generate large numbers of acutely ill or injured people who require immediate medical health care.
Th e Operating Room (OR) is the key department that provides surgeries to victims. Effi cient management and allocation
of scarce medical resources in ORs can improve outcomes for victims of mass casualty events, operating rooms scheduling
deals with determining surgeries sequence and allocating medical resources. Under mass casualty event, operating rooms
scheduling calls for a dynamic scheduling with a wide variety of patients, surgeries and unforeseen emergencies. Dynamic
scheduling does not create or update schedules; instead, the scheduling mechanism is based on decentralized dispatching. Th e
research interest here focuses on an agent-based approach to scheduling of dynamic operating rooms. Th e operating rooms can
be built up by heterogeneous intelligent agents involving patients, surgeries, medical resources, staff s like doctors, nurses and
anesthetists with diverse goals, constraints and behaviors. Th ese agents have emergent behavior in response to disturbances
in the environment and generate fl exible scheduling in a dynamically adaptive way. In order for a multi-agent-system to
solve such distributed operating rooms scheduling problem coherently, agents must communicate amongst themselves and
coordinate their activities to make decisions. Ant colony intelligence is proposed to be combined with local agent coordination
so as to make autonomous agents adaptive to changing circumstances and to give rise to effi cient global performance under
mass casualty events..
- Robot Localization and Map Building | Automation Control | Multi Robot Systems | New Approaches in Automation and Robotics | Robot Manipulators: Trends and Development | Machine Learning | Quest for Artificial Intelligence
Chair
Meenakshi Nadimpalli
Reliable Software Resources Inc, USA
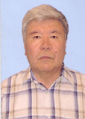
Co-Chair
Ryspek Usubamatov
Kyrgyz Technical University, kyrgyzstan
Session Introduction
Joel M. Haight
University of Pittsburgh, USA
Title: The Design and Use of Adaptive Automated Control Systems; where and how does the human operator optimally fit? Adaptive Automation - State of the Literature and Research Quest
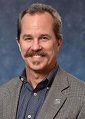
Biography:
Joel M Haight is an Associate Professor of Industrial Engineering at the University of Pittsburgh, USA. He is currently a Professor and Director of the Safety
Engineering program, appointed in 2013. He has spent 4 years as a Research Manager with the U.S. Centers for Disease Control and Prevention (CDC), 10 years
as a Professor and Researcher at the Pennsylvania State University, Department of Energy and Mineral Engineering and nearly 18 years as an Engineer and
Manager at the Chevron Corporation
Abstract:
In today’s technologically driven world, we face the automation paradox. Bainbridge (1983) says that the more automated
a system becomes; the more important it is to consciously and appropriately integrate humans. We cannot argue that
automation provides immeasurable benefi t (improved effi ciency, reliability, accuracy, safety, etc.). However, if humans are not
actively engaged in system operation they experience loss of skill, knowledge, decision-making capability and reaction-time.
Without active engagement in the cognitive-based activities required by a control system, humans become less able to cope,
understand and function correctly. When called upon to take over control in an automated system, we become less capable of
eff ectively operating the system. Adaptive automation is a popular approach to solving this engagement problem. An adaptive
system allows the operator to have control until they are not engaged enough to know what to do in an upset. An NYC Amtrak
engineer derailed a train at 100 mph going into a 50 mph curve. Adaptive speed control gives the engineer the opportunity
to slow down; if no response, the control system takes over and slows the train. Researchers at the University of Pittsburgh
propose a design strategy integrating adaptive control while concurrently minimizing human error-induced incidents. Using
licensed nuclear power plant reactor operators in a control room simulator, researchers identify and measure key biometric
variables while varying task confi guration, automation level and override authority. If impact on system output is predictable,
the generated model can help designers simulate design strategies and resulting impact on system performance, thus providing
more-informed training protocols and content, more-informed simulator practice decisions and improved operational and
operating procedure consistency
Olivier Toupet
NASA Jet Propulsion Laboratory, USA
Title: Fusing wheel and visual odometry with inertial measurements: An Extended Kalman Filter for Unmanned Ground Vehicles in GPS-Denied Enviroments
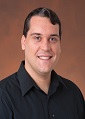
Biography:
Olivier A Toupet has completed his MS in Aeronautics and Astronautics from MIT in 2006. He is currently a Research Technologist in the Robotic Mobility group at
NASA JPL, where he develops advanced autonomy for robotic systems. He is also a Rover Planner for the MSL fl ight mission, where he drives the Curiosity rover
and operates its robotic arm on Mars.
Abstract:
Localization is a central component of a robotic system as many other technologies providing autonomy rely upon it, such as
planning, control, mapping, etc. Smooth and accurate real-time pose estimation is thus a key enabler and many algorithms
exist to provide that capability. One of the most successful and widespread approach is the Extended Kalman Filter (EKF),
which can fuse asynchronous, time-delayed measurements from heterogeneous sensors. It is commonly used in Inertial
Navigation Systems (INS) for combining GPS and IMU measurements. In order to estimate the position and orientation
of an unmanned ground vehicle as it travels through an unknown, unstructured, GPS-denied environment, we leveraged
the EKF framework to fuse the information provided by the vehicle’s onboard gyroscopes, accelerometers, wheel encoders
and cameras. Our implementation is customized for ground vehicles, where the non-holonomic kinematics makes the lateral
motion diffi cult to observe. We use angular rate measurements provided by the IMU’s gyroscopes together with the forward
linear velocity measurement provided by the wheel encoders to predict the vehicle’s motion at a high rate. We then use Visual
Odometry (VO) as a relative pose measurement together with accelerometer measurements provided by the IMU to update
and correct those predictions over time. Our pose estimation system was demonstrated on a real unmanned ground vehicle, a
modifi ed military Humvee, in both short and long-drive scenarios and achieved a performance of less than one percent error
over distance travelled with accumulated yaw drift being the major source of localization error
Mehran Ektesabi
Swinburne University of Technology, Australia
Title: LSSA-CNC- Challenges in Large Scale Subtractive-Additive CNC Machine
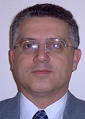
Biography:
Mehran Ektesabi has completed his PhD in 1989. He has more than 30 years of experience in design and development of control and drive systems. Presently, he
is with Faculty of Science, Engineering and Technology at Swinburne University of Technology, Australia. He is an active Member of IEEE, Founder Chair of IEEE
Vehicular Technology Society (VTS) Victorian Chapter and Consular of IEEE branch in Swinburne. His major areas of expertise and research are power electronics,
electric motor control systems, power quality controllers, energy saving and compatibility, renewable energy systems, intelligent and autonomous control, soft
computing adaptive control and system identification
Abstract:
Nowadays, the Large Scale Subtractive-Additive CNC Machines are used in rapid prototyping of superior parts for
very sensitive systems used in aerospace and maritime technology. In this paper, design of a production platform of
a Subtractive-Additive Machine is considered. Th e unit has workspace 2.5×6.5×0.5 meter with two heads that operate
simultaneously. Each of the two processing heads will have 5 DOFs. While one is used for subtractive processing the other
one does the additive processing and both work simultaneously capable of handling the products up to 500 Kg in weight. Th e
Subtractive-Additive machine uses laser deposition welding with powder nozzle where the specimen thickness depends on
size of powder, laser and nozzle geometry. In this study, many of the challenges of large scale systems, such as; large working
area with escalated problems in design and operation, large weight handling of specimen, simultaneous operation of two
heads/multi-heads, which may aff ect the response time and complication of production, eff ects on the precision of movement
by using elevated magnetic bearing system, eff ects on the precision of the size on the end product, complexity of movement
strategy, mutual eff ects of the two heads as integrated, vibration (mechanical as well as electrical EMI) as well as thermal eff ect
and heat treatment during manufacturing has been considered and solutions to overcome such problems are suggested
Silvio Simani
University of Ferrara, Italy
Title: Advanced Issues of Wind Turbine Modelling and Control
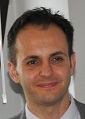
Biography:
Silvio Simani has received the Laurea degree in Electronic Engineering in 1996 and PhD in Information Science (Automatic Control) in 2000. Since 2006, he has
been an IEEE Senior Member and from 2000 a Member of the SAFEPROCESS Technical Committee. Since 2002, he has been working as an Assistant Professor
at the Department of Engineering of the University of Ferrara, Italy. His research interests include fault diagnosis, fault tolerant control and system identifi cation, on
which he published about 200 refereed journal and conference papers, as well as three books and chapters.
Abstract:
The motivation for this talk proposal comes from a real need to have an overview about the challenges of modeling and
control for very demanding systems, such as wind turbine systems, which require reliability, availability, maintainability
and safety over power conversion effi ciency. Th ese issues have begun to stimulate research and development in the wide
control community particularly for these installations that need a high degree of sustainability. Note that this topic represents
a key point mainly for off shore wind turbines with very large rotors, since they are characterized by challenging modeling
and control problems as well as expensive and safety critical maintenance works. In this case, a clear confl ict exists between
ensuring a high degree of availability and reducing maintenance times, which aff ect the fi nal energy cost. On the other hand,
wind turbines have highly nonlinear dynamics with a stochastic and uncontrollable driving force as input in the form of wind
speed, thus representing an interesting challenge also from the modeling point of view. Suitable control methods can provide a
sustainable optimization of the energy conversion effi ciency over wider than normally expected working conditions. Moreover,
a proper mathematical description of the wind turbine system should be able to capture the complete behavior of the process
under monitoring, thus providing an important impact on the control design itself. In this way, the control scheme could
guarantee prescribed performance, whilst also giving a degree of tolerance to possible deviation of characteristic properties
or system parameters from standard conditions, if properly included in the wind turbine model itself. Th e most important
developments in advanced controllers for wind turbines are addressed and open problems in the areas of modeling of wind
turbines are also outlined.
Darian Reyes Fernandez de Bulnes
Tijuana Institute of Technology, Mexico
Title: High-Level Synthesis through metaheuristics and LUTs optimization in FPGA devices
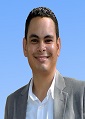
Biography:
Darian Reyes Fernandez de Bulnes is currently a PhD student in Engineering Sciences in the Department of Electrical and Electronics Engineering of the Tijuana
Technological Institute, Mexico. He has received Bachelor’s degree in Computer Science at the University of Computer Science in 2011 and Master's degree in
Computer Science at the University of Havana in 2016, both in Cuba. His research areas include evolutionary computation, multi-objective metaheuristics and
computer-aided design.
Abstract:
Operations scheduling and lookup table (LUT) based technology mapping are fundamental problems of mapping designs
onto an electronic device, such as a fi eld programmable gate array. We present an approach to apply two optimizations
consecutively. In fi rst optimization, we apply several metaheuristic algorithms for multi-objective optimization at the high-level
synthesis stage. And in second optimization, we realize reductions of LUTs at the logic synthesis stage. Several circuit designs
are represented in a data fl ow graph (DFG) and the experiments are carried out on the standard Mediabench benchmark. In
the fi rst optimization, we compared NSGA-II, FEMO, HypE, IBEA, SPEA2 and WSGA. Results have an average improvement
14.06% in occupied area and 7.01% in power consumption. Th en, optimized DFG schedules are converted into very high
description language code using the Xilinx ISE design suite tool. Later, in the second optimization, the IMap algorithm is used
to obtain combinational area reductions. Results show that 60% of the circuits are improved in comparison with the Xilinx ISE
design suite.